Szybkość korozji to wieloczynnikowy parametr, który zależy zarówno od zewnętrznych warunków środowiskowych, jak i wewnętrznych właściwości materiału. W dokumentacji normatywno-technicznej istnieją pewne ograniczenia dotyczące dopuszczalnych wartości zniszczenia metalu podczas eksploatacji urządzeń i konstrukcji budowlanych, aby zapewnić ich bezawaryjną eksploatację. W inżynierii nie ma uniwersalnej metody określania szybkości korozji. Wynika to ze złożoności uwzględnienia wszystkich czynników. Najbardziej wiarygodną metodą jest badanie historii działania obiektu.
Kryteria
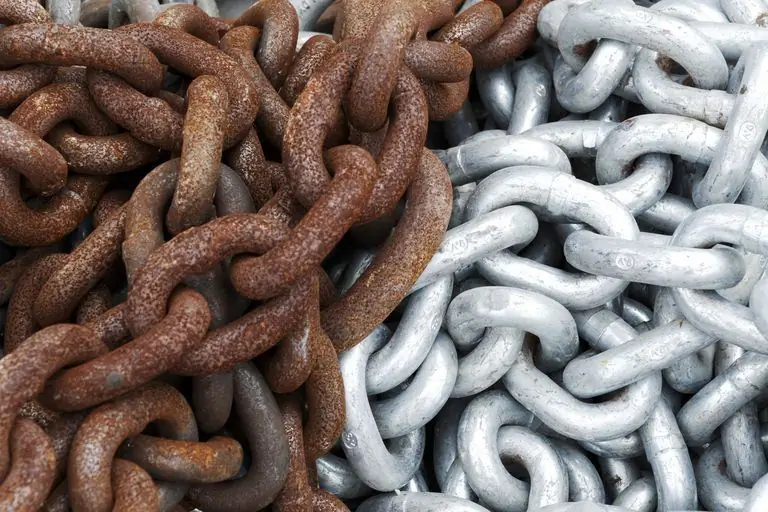
Obecnie w projektowaniu inżynierskim stosuje się kilka szybkości korozji:
- Zgodnie z bezpośrednią metodą oceny: zmniejszenie masy części metalowej na jednostkę powierzchni - wskaźnik masy (mierzony w gramach na 1 m2 przez 1 godzinę); głębokość uszkodzenia (lub przepuszczalność procesu korozyjnego), mm/rok; ilość uwolnionej fazy gazowej produktów korozji; czas, w którym pojawia się pierwsze uszkodzenie korozyjne; liczba ognisk korozji na jednostkę powierzchnipowierzchnie, które pojawiły się w określonym czasie.
- Szacowane pośrednio: siła prądu korozji elektrochemicznej; opór elektryczny; zmiana właściwości fizycznych i mechanicznych.
Pierwszy wskaźnik wyceny bezpośredniej jest najbardziej powszechny.
Wzory obliczeniowe
W ogólnym przypadku ubytek masy, który określa szybkość korozji metalu, określa następujący wzór:
Vkp=q/(St), gdzie q jest spadkiem masy metalu, g;
S - powierzchnia, z której został przeniesiony materiał, m2;
t - okres czasu, godziny
Dla blachy i wykonanych z niej skorup, określ wskaźnik głębokości (mm/rok):
H=m/t, m to głębokość penetracji metalu.
Istnieje następujący związek między pierwszym i drugim wskaźnikiem opisanym powyżej:
H=8, 76Vkp/ρ, gdzie ρ jest gęstością materiału.
Główne czynniki wpływające na szybkość korozji
Na tempo niszczenia metalu wpływają następujące grupy czynników:
- wewnętrzne, związane z fizyczną i chemiczną naturą materiału (struktura faz, skład chemiczny, chropowatość powierzchni części, naprężenia szczątkowe i eksploatacyjne w materiale i inne);
- zewnętrzne (warunki środowiskowe, prędkość ruchu czynnika korozyjnego, temperatura, skład atmosfery, obecność inhibitorów lub stymulatorów i inne);
- mechaniczne (powstawanie pęknięć korozyjnych, niszczenie metalu pod wpływem obciążeń cyklicznych,kawitacja i korozja cierna);
- cechy konstrukcyjne (wybór gatunku metalu, odstępy między częściami, wymagania dotyczące chropowatości).
Właściwości fizyczne i chemiczne
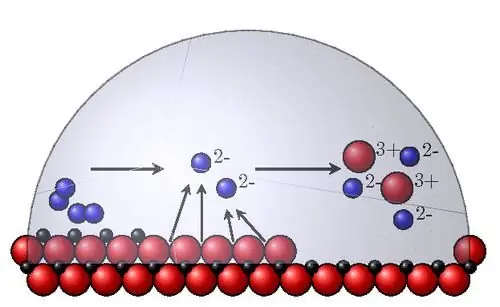
Najważniejszymi czynnikami korozji wewnętrznej są:
- Stabilność termodynamiczna. Do oznaczenia tego w roztworach wodnych stosuje się wykresy odniesienia Pourbaixa, wzdłuż osi odciętej, na której kreślone jest pH ośrodka, a wzdłuż osi rzędnych potencjał redoks. Potencjalne przesunięcie w kierunku dodatnim oznacza większą stabilność materiału. Wstępnie definiuje się go jako normalny potencjał równowagi metalu. W rzeczywistości materiały korodują w różnym tempie.
- Pozycja atomu w układzie okresowym pierwiastków chemicznych. Metalami najbardziej podatnymi na korozję są metale alkaliczne i metale ziem alkalicznych. Szybkość korozji spada wraz ze wzrostem liczby atomowej.
- Struktura kryształu. Ma niejednoznaczny wpływ na zniszczenie. Sama gruboziarnista struktura nie prowadzi do wzrostu korozji, ale sprzyja rozwojowi międzykrystalicznego selektywnego niszczenia granic ziaren. Metale i stopy o jednorodnym rozkładzie faz korodują równomiernie, natomiast te o nierównomiernym rozkładzie korodują zgodnie z mechanizmem ogniskowym. Wzajemne ułożenie faz pełni funkcję anody i katody w agresywnym środowisku.
- Niejednorodność energetyczna atomów w sieci krystalicznej. Atomy o najwyższej energii znajdują się w rogach twarzymikronierówności i są aktywnymi centrami rozpuszczania podczas korozji chemicznej. Dlatego staranna obróbka części metalowych (szlifowanie, polerowanie, wykańczanie) zwiększa odporność na korozję. Efekt ten można również wyjaśnić tworzeniem gęstszych i bardziej ciągłych warstw tlenków na gładkich powierzchniach.
Wpływ średniej kwasowości
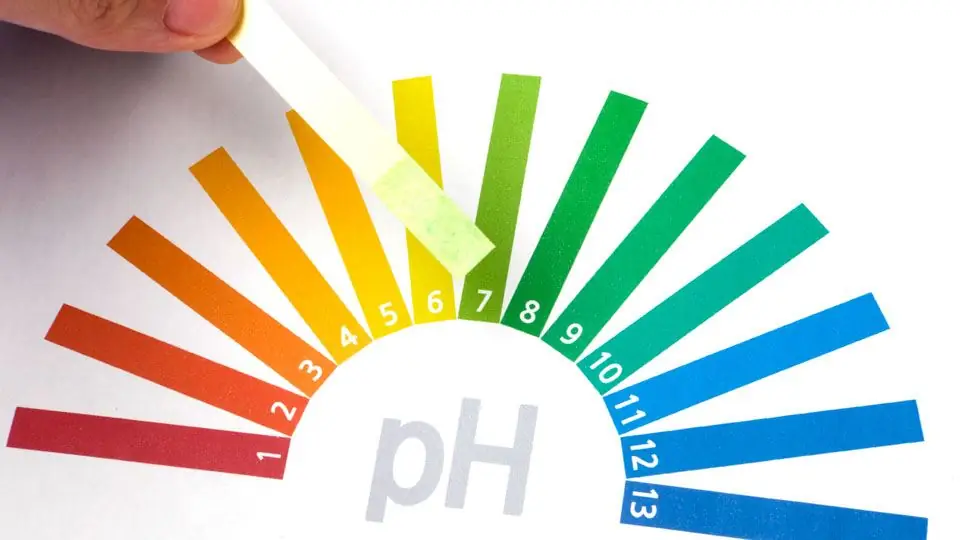
W procesie korozji chemicznej stężenie jonów wodorowych wpływa na następujące punkty:
- rozpuszczalność produktów korozji;
- tworzenie ochronnych warstw tlenkowych;
- wskaźnik niszczenia metalu.
Kiedy pH jest w zakresie 4-10 jednostek (roztwór kwaśny), korozja żelaza zależy od intensywności przenikania tlenu do powierzchni obiektu. W roztworach alkalicznych szybkość korozji najpierw maleje z powodu pasywacji powierzchni, a następnie przy pH >13 wzrasta w wyniku rozpuszczenia ochronnej warstwy tlenkowej.
Dla każdego rodzaju metalu istnieje własna zależność intensywności destrukcji od kwasowości roztworu. Metale szlachetne (Pt, Ag, Au) są odporne na korozję w środowisku kwaśnym. Zn, Al są szybko niszczone zarówno w kwasach, jak i zasadach. Ni i Cd są odporne na zasady, ale łatwo korodują w kwasach.
Skład i stężenie roztworów obojętnych
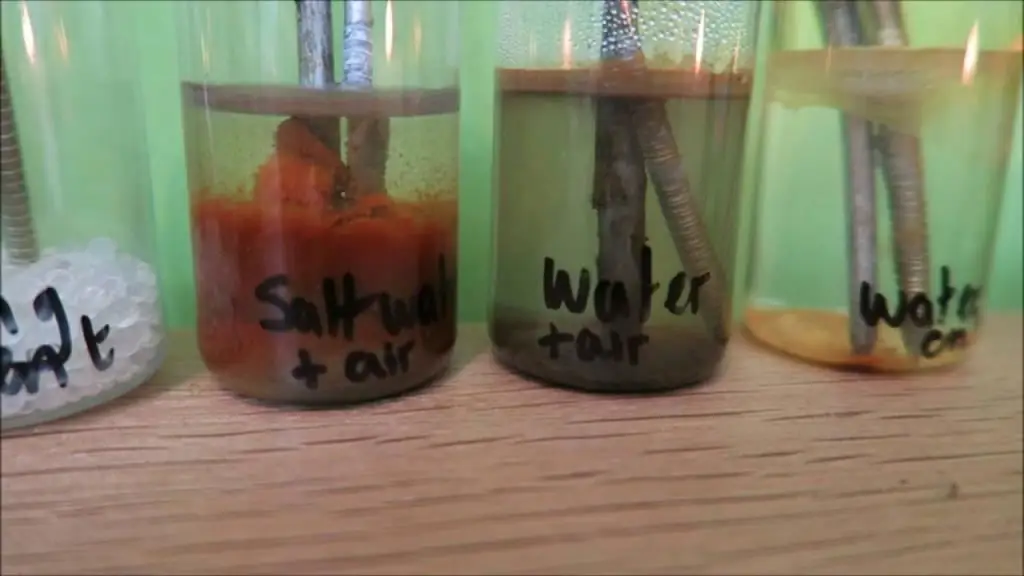
Szybkość korozji w roztworach obojętnych zależy bardziej od właściwości soli i jej stężenia:
- Podczas hydrolizy soli ww środowisku korozyjnym powstają jony, które działają jako aktywatory lub opóźniacze (inhibitory) niszczenia metali.
- Związki zwiększające pH zwiększają również tempo procesu destrukcyjnego (np. soda kalcynowana), a te, które obniżają kwasowość obniżają ją (chlorek amonu).
- W obecności chlorków i siarczanów w roztworze, niszczenie jest aktywowane aż do osiągnięcia określonego stężenia soli (co tłumaczy się intensyfikacją procesu anodowego pod wpływem jonów chlorkowych i siarkowych) oraz następnie stopniowo maleje z powodu spadku rozpuszczalności tlenu.
Niektóre rodzaje soli mogą tworzyć nierozpuszczalny film (np. fosforan żelaza). Pomaga to chronić metal przed dalszym zniszczeniem. Ta właściwość jest używana podczas stosowania neutralizatorów rdzy.
Inhibitory korozji
Inhibitory korozji (lub inhibitory) różnią się mechanizmem działania na proces redoks:
- Anoda. Dzięki nim powstaje film pasywny. Do tej grupy należą związki na bazie chromianów i dwuchromianów, azotanów i azotynów. Ostatni rodzaj inhibitorów służy do międzyoperacyjnej ochrony części. W przypadku stosowania anodowych inhibitorów korozji należy najpierw określić ich minimalne stężenie ochronne, gdyż dodawanie małych ilości może prowadzić do zwiększenia szybkości niszczenia.
- Katoda. Mechanizm ich działania opiera się na obniżeniu stężenia tlenu i odpowiednio spowolnieniu procesu katodowego.
- Osłanianie. Inhibitory te izolują powierzchnię metalu, tworząc nierozpuszczalne związki, które osadzają się jako warstwa ochronna.
Ostatnia grupa obejmuje neutralizatory rdzy, które są również używane do czyszczenia tlenków. Zwykle zawierają kwas fosforowy. Pod jego wpływem dochodzi do fosforanowania metali - tworzenia silnej warstwy ochronnej nierozpuszczalnych fosforanów. Neutralizatory nakłada się pistoletem natryskowym lub wałkiem. Po 25-30 minutach powierzchnia nabiera biało-szarego koloru. Po wyschnięciu kompozycji nakładane są farby i lakiery.
Działanie mechaniczne
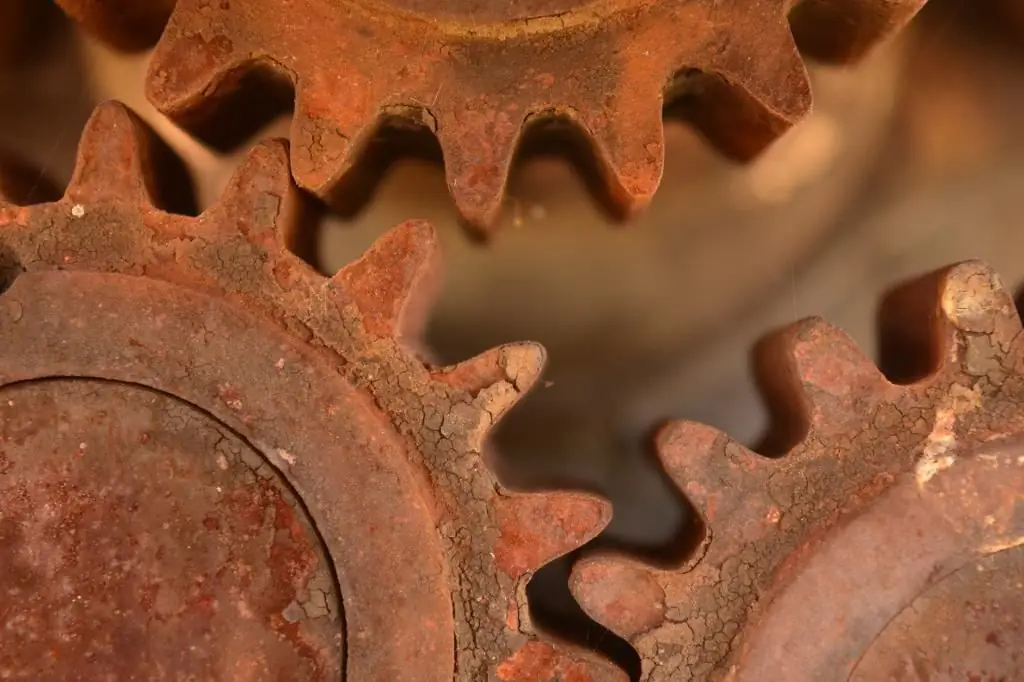
Wzrost korozji w agresywnym środowisku jest ułatwiony przez takie rodzaje działań mechanicznych, jak:
- Naprężenia wewnętrzne (podczas formowania lub obróbki cieplnej) i zewnętrzne (pod wpływem obciążenia przyłożonego z zewnątrz). W efekcie dochodzi do niejednorodności elektrochemicznej, zmniejsza się stabilność termodynamiczna materiału i powstaje pękanie korozyjne. Szczególnie szybkie jest niszczenie pod obciążeniem rozciągającym (pęknięcia powstają w prostopadłych płaszczyznach) w obecności anionów utleniających, np. NaCl. Typowym przykładem urządzeń podlegających tego typu zniszczeniom są części kotłów parowych.
- Zmienne działanie dynamiczne, wibracje (zmęczenie korozyjne). Następuje intensywne obniżenie granicy zmęczenia, powstają liczne mikropęknięcia, które następnie łączą się w jedno duże. Numercykle do zniszczenia w większym stopniu zależą od składu chemicznego i fazowego metali i stopów. Osie pomp, sprężyny, łopatki turbin i inne urządzenia podlegają takiej korozji.
- Tarcie części. Szybka korozja spowodowana jest mechanicznym zużyciem folii ochronnych na powierzchni części oraz oddziaływaniem chemicznym z otoczeniem. W cieczy szybkość niszczenia jest mniejsza niż w powietrzu.
- Wpływ kawitacji. Kawitacja występuje, gdy ciągłość przepływu cieczy zostaje naruszona w wyniku tworzenia się pęcherzyków próżniowych, które zapadają się i tworzą efekt pulsacyjny. W efekcie dochodzi do głębokich zniszczeń o charakterze lokalnym. Ten rodzaj korozji jest często spotykany w aparaturze chemicznej.
Czynniki projektowe
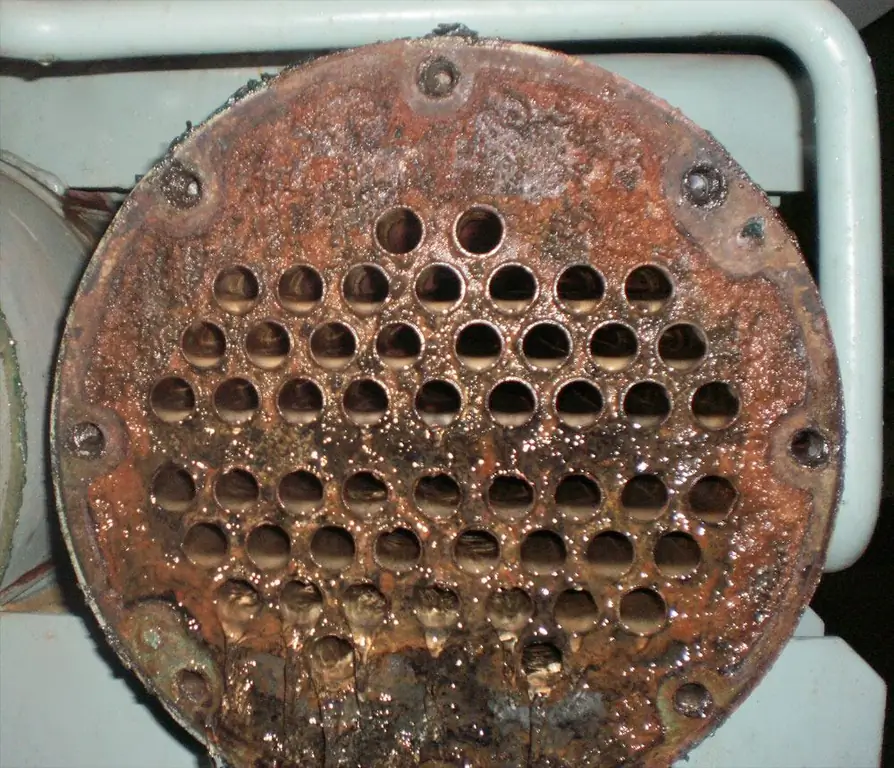
Projektując elementy pracujące w agresywnych warunkach należy wziąć pod uwagę, że szybkość korozji wzrasta w następujących przypadkach:
- gdy różne metale wchodzą w kontakt (im większa różnica potencjałów elektrod między nimi, tym wyższa siła prądu elektrochemicznego procesu niszczenia);
- w obecności koncentratorów naprężeń mechanicznych (rowki, rowki, otwory i inne);
- o niskiej czystości obrabianej powierzchni, ponieważ powoduje to miejscowe zwarcie par galwanicznych;
- ze znaczną różnicą temperatur poszczególnych części aparatu (powstają ogniwa cieplne galwaniczne);
- w obecności stref stagnacji (szczeliny, luki);
- podczas formowanianaprężenia szczątkowe, zwłaszcza w złączach spawanych (w celu ich wyeliminowania należy zapewnić obróbkę cieplną - wyżarzanie).
Metody oceny
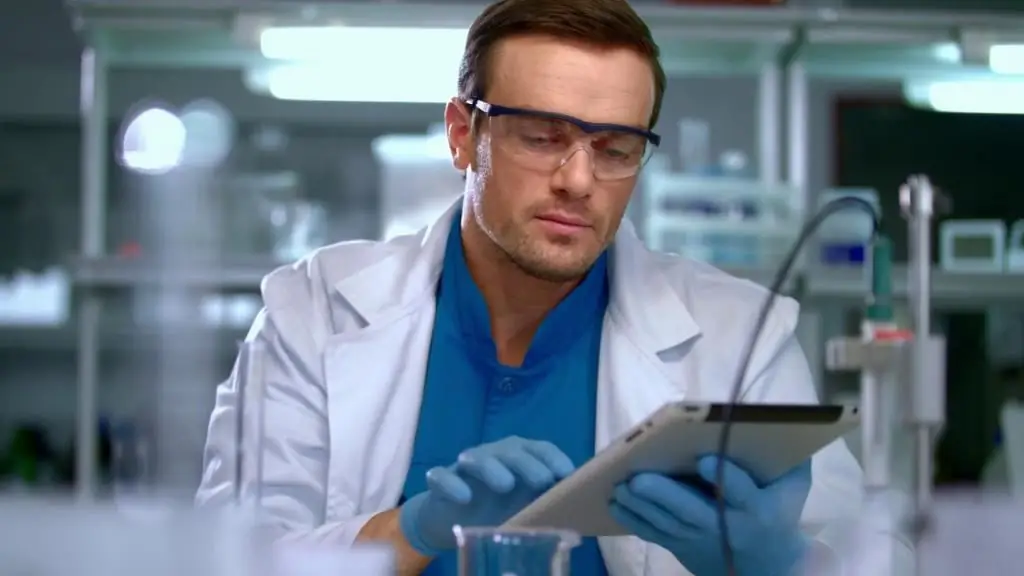
Istnieje kilka sposobów oceny szybkości niszczenia metali w agresywnym środowisku:
- Laboratorium - testowanie próbek w sztucznie symulowanych warunkach zbliżonych do rzeczywistych. Ich zaletą jest to, że pozwalają skrócić czas badania.
- Pole - odbywają się w naturalnych warunkach. Zajmują im dużo czasu. Zaletą tej metody jest uzyskanie informacji o właściwościach metalu w warunkach dalszej eksploatacji.
- Testowanie in-situ gotowych metalowych przedmiotów w środowisku naturalnym.